An ERP System Review is NOT a Report Card
It's a no-judgment-review - we promise!
We all remember our school days and the nervousness that we felt when it came time to get our grades. Even if we were doing well, we were still nervous. Sometimes we experienced that same nervousness when it came time for a performance review on our job. Nervousness…sometimes dread…knowing that our performance was not what we wanted it to be, or others expected it to be.
Somehow I think the feelings that we felt in our past often find ways to creep into our present. I have seen this recently when I suggested an ERP system review to one of our customers. They immediately became flustered and thought about every possible problem that they knew existed within the software and how they were currently using it. I asked them to consider the purpose of the ERP system review.
An ERP Utilization Review will:
- Document how your company is using your ERP system (or a particular aspect of the system) and to what extent the system meets the needs of the business.
- Identify challenges encountered using the software.
- Create opportunities for improving business processes and generating additional value.
- Identify potential risks and areas that need improvement.
So, if the result of ERP system review is to establish a path forward for growth based on current status, then why doesn’t every company take advantage of it? I think for some, the answer lies in the feelings of nervousness and dread still stuck in the recesses of our brains.
An ERP system review or more specifically a utilization review is NOT a personal report card, or performance review showing how well a particular individual does his/hers/their job, nor is it an attack on the team that implemented the software.
As they say, hindsight is 20/20. What we view now to be a less than ideal implementation methodology may have been absolutely appropriate at the time the software was originally deployed. The software has likely matured and the skillsets of the individuals responsible for the system have likely matured as well. In some cases, those resources are no longer with the company, leaving those that remain with no back story as to how and why implementation decisions were made.
Instead of viewing the ERP utilization review as a reason to find fault in previous decisions, think of it as discovering untapped potential – both of the ERP system and the people who use it. Viewing an ERP utilization review in this way puts a positive spin on it and allows us to challenge ourselves to identify opportunities for growth far greater than anything we imagined before. This means not only moving our businesses forward faster but also advancing the strength of the company as individuals and as a team.
What untapped potential lies within your company?
Consider a utilization review of your entire ERP system, or just a part of it like Finance, Technology, Materials Management, Order Processing, or Shop Floor Control. You just might be surprised at what greatness can be achieved… far greater than anyone could have imagined.
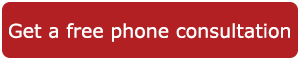
800.762.2077